What is Porosity in Welding: Comprehending Its Reasons and Enhancing Your Abilities
Wiki Article
Unwinding the Mystery of Porosity in Welding: Tips for Lessening Issues and Maximizing Quality
In the elaborate world of welding, porosity remains a consistent difficulty that can considerably affect the high quality and stability of welded joints. As we delve right into the midsts of porosity in welding, revealing the tricks to its avoidance and control will be critical for experts seeking to master the art of premium weldments.Understanding Porosity in Welding
Porosity in welding, a common concern run into by welders, describes the existence of gas pockets or spaces in the welded product, which can endanger the integrity and quality of the weld. These gas pockets are generally trapped throughout the welding procedure because of various factors such as inappropriate securing gas, contaminated base products, or inaccurate welding parameters. The development of porosity can deteriorate the weld, making it prone to breaking and corrosion, ultimately causing architectural failings.By recognizing the significance of preserving proper gas securing, making certain the sanitation of base products, and enhancing welding setups, welders can considerably minimize the likelihood of porosity formation. Generally, a thorough understanding of porosity in welding is vital for welders to produce high-grade and durable welds.
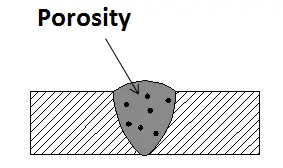
Common Sources Of Porosity
When evaluating welding procedures for possible high quality problems, comprehending the typical causes of porosity is important for maintaining weld integrity and preventing architectural failings. Porosity, defined by the existence of cavities or voids in the weld steel, can dramatically jeopardize the mechanical residential properties of a welded joint.
Another prevalent source of porosity is the existence of moisture and contaminants externally of the base metal or filler material. When welding materials are not correctly cleaned or are revealed to high degrees of humidity, the evaporation of these pollutants during welding can develop spaces within the weld bead. Additionally, welding at inappropriate specifications, such as excessively high traveling speeds or currents, can create extreme turbulence in the weld swimming pool, trapping gases and causing porosity. By resolving these typical reasons with proper gas securing, material prep work, and adherence to optimal welding criteria, welders can reduce porosity and enhance the high quality of their welds.
Techniques for Porosity Prevention
Applying effective precautionary measures is vital in reducing the incident of porosity in welding procedures. One technique for porosity avoidance is making certain proper cleaning of the base metal prior to welding. Impurities such as oil, grease, rust, and paint can cause porosity, so thorough cleaning utilizing ideal solvents or mechanical techniques is crucial.
Utilizing top notch filler products and protecting gases that are view publisher site appropriate for the base metal and welding process can considerably reduce the risk of porosity. In addition, keeping correct welding criteria, such as voltage, present, travel rate, and gas circulation rate, is important for porosity prevention.
In addition, using appropriate welding methods, such as maintaining a regular traveling speed, electrode angle, and arc length, can aid stop porosity (What is Porosity). Sufficient training of welders to ensure they adhere to finest techniques and top quality control procedures is also essential in decreasing porosity flaws in welding

Best Practices for High Quality Welds
Ensuring adherence to industry criteria and appropriate weld joint preparation are basic elements of achieving continually high-grade welds. Along with these foundational steps, there are a number of best techniques that welders can carry out to further boost the high quality of their welds. One trick method is keeping appropriate cleanliness in the welding location. Contaminants such as oil, oil, rust, and paint can detrimentally affect the top quality of the weld, resulting in issues. Completely cleaning the workpiece and surrounding location prior to welding can assist mitigate these concerns.An additional finest technique is to carefully pick the suitable welding criteria for the particular materials being signed up with. This includes setting the proper voltage, current, travel rate, and securing gas circulation rate. Proper specification option ensures optimal weld infiltration, blend, and total quality. Utilizing high-grade welding consumables, such as electrodes and filler steels, can significantly impact the final weld quality. Spending in costs consumables can lead to more powerful, extra sturdy welds with less defects. By following these best practices, welders can consistently create premium welds that satisfy market requirements and surpass client expectations.
Significance of Porosity Control
Porosity control plays an essential role in making certain the stability and quality of welding joints. Porosity, identified by the existence of cavities or gaps Learn More Here within the weld metal, can considerably endanger the mechanical residential or commercial properties and structural honesty of the weld. Extreme porosity compromises the weld, making it more at risk to splitting, corrosion, and total failure under functional tons.Reliable porosity control is crucial for preserving the wanted mechanical residential properties, such as strength, ductility, and durability, of the bonded joint. What is Porosity. By reducing porosity, welders can boost the overall quality and integrity of the weld, ensuring that it fulfills the efficiency requirements of the designated application
Furthermore, porosity control is important for accomplishing the wanted aesthetic appearance of the weld. Excessive porosity not just deteriorates the weld yet also diminishes its aesthetic allure, which can be crucial in markets where visual appeals are necessary. Proper porosity control methods, such as utilizing the proper securing gas, controlling the welding parameters, and making sure appropriate sanitation of the base products, are necessary for generating top quality welds with very little problems.
Conclusion
Finally, porosity in welding is a typical flaw that can endanger the top quality of the weld. By comprehending the sources of porosity and applying correct prevention this content methods, welders can minimize problems and achieve higher high quality welds. It is necessary to regulate porosity in welding to make certain the honesty and strength of the final product. Executing ideal methods for porosity control is important for achieving optimal welding results.Report this wiki page